Businesses are increasingly automating their mold-making applications to stay competitive in an increasingly global market. Automation enables manufacturers to enhance precision and consistency in their products, a critical factor in industries where mold accuracy directly impacts product quality. Additionally, automation offers significant cost savings over time by reducing labor expenses and minimizing material waste through more efficient use of resources.
The adoption of these technologies also allows for increased production capacity without a proportional increase in labor costs, enabling businesses to scale their operations effectively. Furthermore, by automating repetitive and physically demanding tasks, companies can improve workplace safety and employee satisfaction. This strategic move not only aligns with the goals of increasing efficiency and reducing costs but also helps in adhering to stringent quality standards required by customers in industries such as automotive, aerospace, and healthcare.
How are robots used in mold-making?
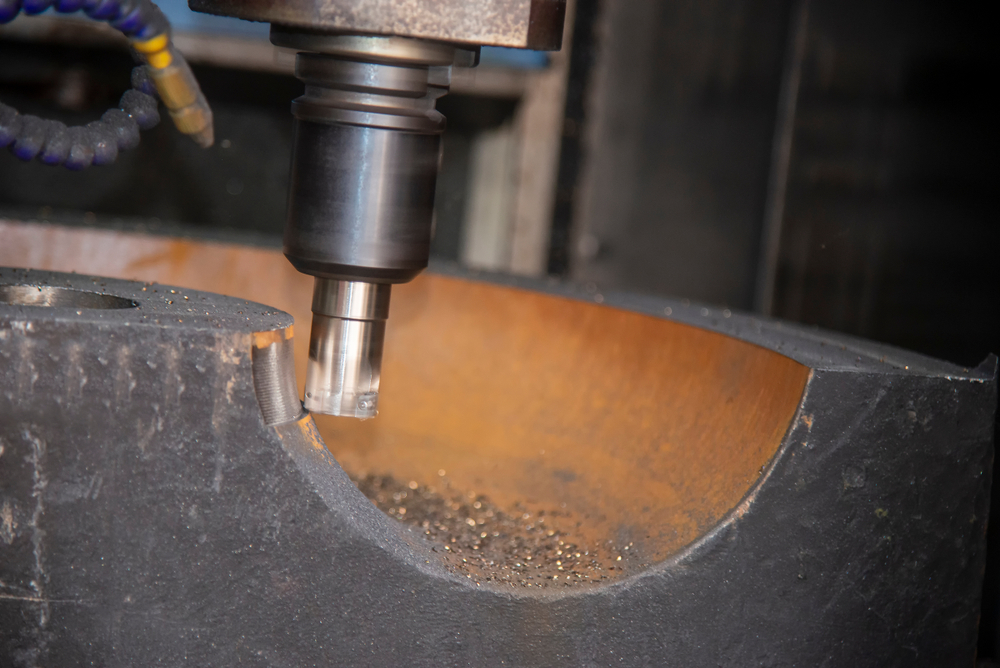
Integrating robotics and Computer Numerical Control (CNC) machines in the mold-making process has become much more prevalent over time, enhancing efficiency, precision, and flexibility. Let’s look at some examples of robotics applications in mold-making applications and the pros and cons of automating these tasks.
Design and prototyping
Businesses use 3D printing robots for rapid prototyping. Automation significantly reduces the time from design to prototype, allowing quick iterations and adjustments. It also lowers the cost of prototyping complex mold designs. However, the initial setup and material costs can be high, and the resolution may not match final production methods for very detailed prototypes.
Material handling and loading
Automated gantry systems are helpful for moving raw materials. This increases efficiency and reduces human labor in repetitive and physically demanding tasks. Automation also minimizes the risk of injury and material damage. However, Gantry systems can be incredibly expensive, so they require high initial investment and significant space for installation. The variability of material shapes and sizes limits the system's effectiveness.
Milling and machining
CNC milling machines are commonly used for mold fabrication. CNC machines offer high precision and repeatability, capable of producing complex molds with tight tolerances. They can operate continuously with minimal supervision. On the flip side, the complexity of programming and setup for each new mold design can prove challenging for untrained staff. Additionally, the high initial cost of equipment and maintenance should be considered to ensure this investment is ROI-positive.
Injection mold filling
Robotic arms equipped with injection nozzles can be used for filling molds. Robots provide consistent and precise filling of molds, reducing waste and improving the quality of the final product. They can also be programmed for various materials and mold designs. However, setup and programming can be complex, requiring expertise. Additionally, this solution may not be suitable for all materials, especially those with unique handling properties, such as certain types of thermoplastics.
Finishing and polishing
It is common for manufacturers to automate finishing cells with robotic arms. Robots deliver uniform surface finishes, improving product aesthetics and function. They also reduce the need for manual labor and exposure to hazardous materials. Robots, however, may struggle with complex geometries that require detailed hand finishing. And like other automation solutions, initial setup and programming require time and expertise.
Inspection and quality control
Robots equipped with vision systems can be used for automated inspection. Automating these tasks enhances quality control by providing consistent, detailed inspections at high speeds. Additionally, businesses can reduce the impact of human error and increase overall throughput. However, the complexity of setting up inspection criteria and the high cost of advanced vision systems can be prohibitive. Manufacturers should expect ongoing adjustments for different mold types.
Assembly and packaging
Manufacturers can use collaborative robots (cobots) for assembling and packaging finished molds. Cobots can work alongside human workers, increasing productivity while reducing the risk of injury. They are lighter, more flexible, and easily reprogrammed for different tasks. It should be noted that cobots are limited by their payload capacity and speed, which may not match traditional assembly line speeds. Manufacturers should carefully plan to integrate cobots smoothly and effectively with human workflows.
By automating these applications, manufacturers can achieve significant improvements in mold-making processes. However, each solution comes with its own challenges and considerations, necessitating a balanced approach to adopting robotics and CNC technologies.
What types of robots exist?
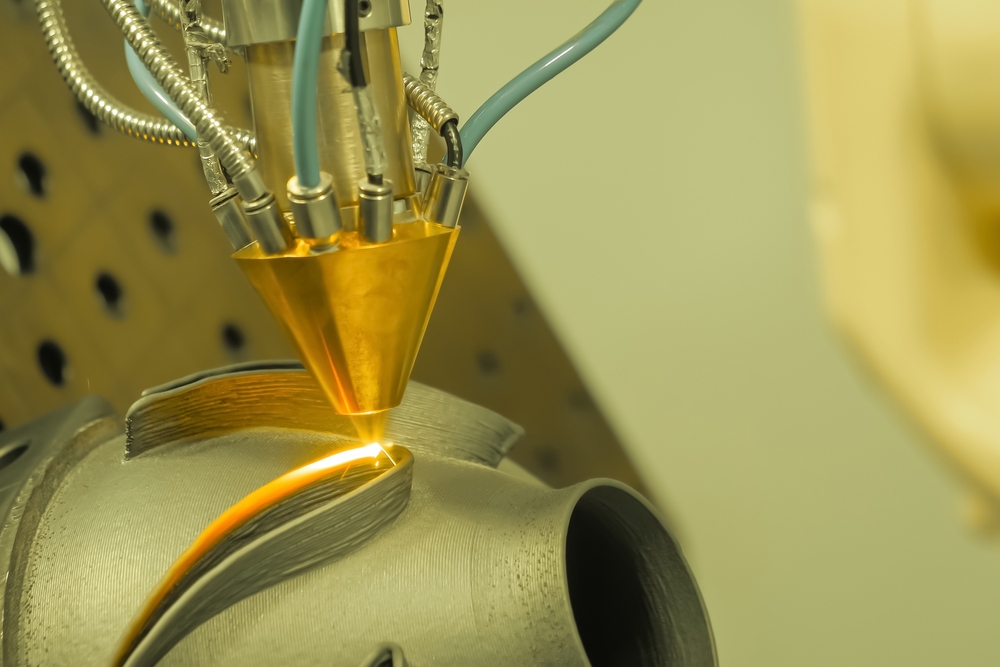
In the context of mold-making, several types of robots and machinery are commonly used, each serving different functions within the production process.
Articulated robots
Articulated robots have rotary joints and can range from simple two-joint structures to complex models with ten or more interacting joints, ideal for tasks requiring high flexibility and precision.
Cartesian robots
Also known as linear robots, cartesian robots operate in straight lines along the X, Y, and Z axes. They are often used for material handling and simple assembly tasks where precision and speed are key.
SCARA robots
SCARA robots are selective compliance assembly robot arms designed for high-speed assembly tasks. Its rigid vertical axis and flexible horizontal movements make it well-suited for picking, placing, and assembly operations in mold-making.
Collaborative robots (cobots)
Cobots are designed to work alongside human operators, assisting with tasks that require more flexibility or detailed attention. They are equipped with safety features to ensure human workers are not harmed.
CNC machines
CNC machines play a crucial role in mold-making, automating the cutting, milling, and drilling processes with exceptional precision. Controlled by computer programming, CNC machines can produce complex shapes and high-quality molds with minimal human intervention. Their ability to work with various materials and maintain consistent accuracy makes CNC machines indispensable in modern mold-making operations.
Together, these robots and CNC machines form a powerful arsenal for manufacturers, combining the strengths of automation, precision, and flexibility. By leveraging these technologies, mold-making processes become more efficient, accurate, and adaptable to the changing demands of the manufacturing landscape.
What are the advantages of robotic mold-making
The integration of robotics into mold-making offers numerous advantages that significantly enhance production capabilities. Here are some specific examples:
Increased efficiency and productivity
Robots can operate 24/7, leading to a substantial increase in production output. For example, a robotic arm equipped with milling tools can produce molds around the clock, reducing production times–which are commonly on the scale of weeks–for complex parts and potentially unlocking lights-out production.
Enhanced precision and quality
The precision of robotic systems is unparalleled, capable of achieving tolerances within fractions of a millimeter. This level of accuracy ensures that each mold is of the highest quality, with minimal variances between products. For instance, in the automotive industry, where precision is paramount, robots can produce molds for car parts that fit perfectly every time, reducing waste and rework.
Reduced labor costs
By automating repetitive tasks, companies can significantly reduce the labor costs associated with mold-making. A single robot can perform the work of several people, leading to savings in applied labor to individual molds.
Safety
Furthermore, robots can work in environments that might be hazardous to humans, such as those with toxic materials or extreme temperatures, thereby reducing the risk to people working in the mold-making process.
Flexibility
Robots can be quickly reprogrammed and fitted with different tools to take on various tasks, making them highly adaptable to changing production needs. For example, a robot that polishes molds can be easily reprogrammed to perform detailed engraving, allowing manufacturers to respond swiftly to custom orders or design changes. This is a critical feature relevant to today’s labor pool challenges.
What are the limitations of robotic mold-making?
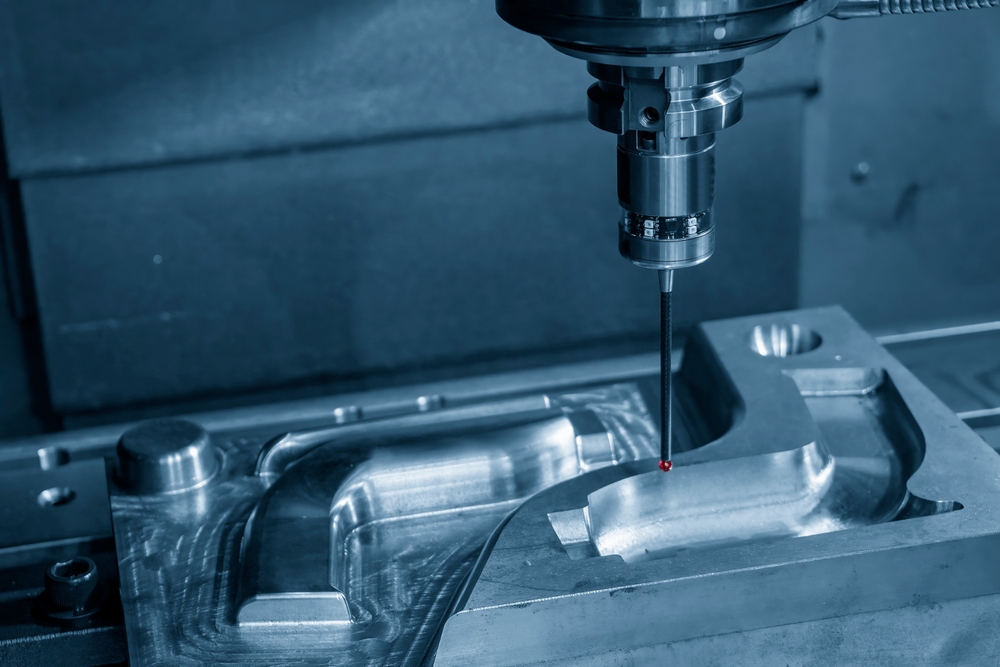
Despite the significant benefits, there are also robotic mold-making limitations that manufacturers must consider.
High initial investment
The investment in purchasing, installing, and integrating robotic systems into existing manufacturing processes is significant but should be viewed as a strategic investment in efficiency and long-term growth. It’s important for small and medium-sized enterprises (SMEs) to consider the broader picture of return on investment (ROI).
A thorough analysis of the potential productivity increases, cost reductions, and product quality improvements can reveal that the upfront investment in robotic technologies can be recuperated over time. Additionally, understanding the total ROI helps mitigate concerns about the initial expenditure, making it a more manageable decision for businesses aiming to stay competitive and innovative in the market.
Technical complexity
Implementing robotic systems requires a certain level of technical expertise, both in programming and maintaining the robots. Manufacturers may need to invest in training for their staff or hire specialized personnel, which can add to the overall cost of adopting robotic mold-making solutions. Alternatively, partnering with suppliers and 3rd party integrators can help manufacturers fill in gaps with their technical staff.
Limited to repetitive tasks
While robots excel at performing repetitive, predefined tasks, many lack the ability to make complex decisions or adapt to unexpected changes in the production process. For example, if a material behaves unpredictably during the molding process, a human technician may be better equipped to adjust the parameters on the fly than a pre-programmed robot.
Dependency on consistent quality of input materials
Robotic systems require consistent quality of raw materials to operate efficiently. Variations in material properties can affect the final product's quality, necessitating human intervention to adjust the process parameters. This reliance on consistent input quality can be challenging in environments where material properties vary significantly.
By understanding both the advantages and limitations of robotic mold-making, manufacturers can make informed decisions about integrating these technologies into their production processes. This balanced approach enables them to leverage the benefits of automation while mitigating its challenges, ultimately leading to more efficient, flexible, and cost-effective mold-making operations.
How big is the market?
The market for robotics in mold-making is growing rapidly, driven by the demand for efficiency, precision, and flexibility in manufacturing. The market was estimated to be $6.46 Bn (USD) in 2021 and is expected to reach $16.45 Bn (USD) in 2029 at a CAGR of 12.39%.
What’s next?
You may be ready to take the next step towards including robots in your mold-making operations, but where do you start?
The HowToRobot platform connects buyers of automation with a variety of suppliers in a streamlined, easy-to-use environment.
Post your project on HowToRobot today for free, and begin receiving offers from vetted, relevant automation vendors from our supplier network.